The wood Senna frame is made from high quality Baltic Birch Plywood. It is cabinet grade plywood and built to last. If you ask any builder if a substitute can be used, more than likely, the response will be, Baltic Birch is best.
For this video, I used my MDF templates. I recommend if making a frame from templates, use 1/2″ MDF. The 1/4 has to much give to it and mushrooms at the top. The 1/2″ allows the bearing to sit in the middle and not mushroom the ends. It is also a good idea to use the templates as outline drawings and trim each piece of wood first with a band saw or jig saw. This makes the process go alot faster and will not destroy bits as fast.
If you have skins, this will help make a frame. The important thing is the upright placement. The best way to achieve this is to make a template of just the slots with a cutout of 1.26″ according to the bottom plate plans . Remember, this is to fit the entire depth of the uprights. If you use a router the total slot length will be longer to accommodate radius of the bit.
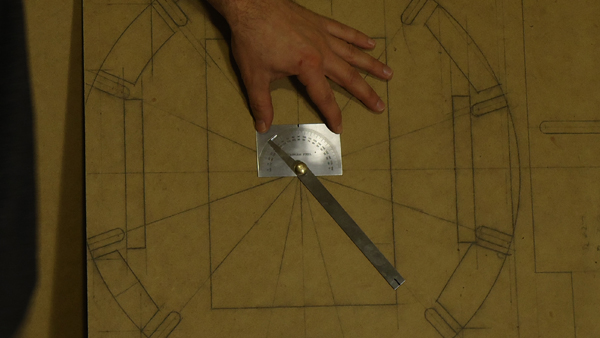
The use of a digital protractor will be easier to make the proper marks.
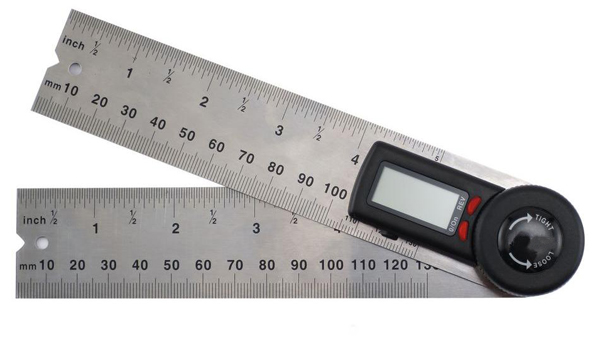
The compass marks are just to show roughly how far you need to make your cuts when using a router.

Make sure you have the centers located and properly marked. This will help with making future cuts.

Start with the uprights. In the video, I show all the uprights drawn out. Since then, I discovered it is easier to make one upright with as many slots cut out as possible and use this as a rough template. This makes it easier to guarantee proper alignment, since you are using the same slots instead of drawing out each one like I previously did.
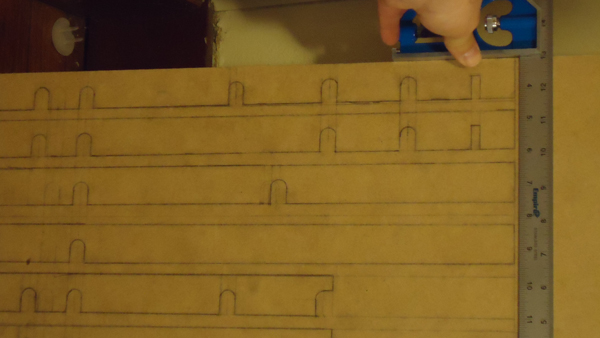
In the above, all slots are marked out. This is not as necessary. If you use a router and cut your wood uprights just bigger than plan, you can use the longest upright as a guide to create all the others. Just work slow with the router and remember what slots you are cutting first, and to raise and lower the bearing bit accordingly. As long as the flat side stays flat, messing up what slots go where is not a big deal. The flat side is where the skins attach so that is more important.
Secure all templates with double sided tape. Make sure the ends have tape and use it frequently to keep the template and work piece from shifting. Never reuse any piece of tape.
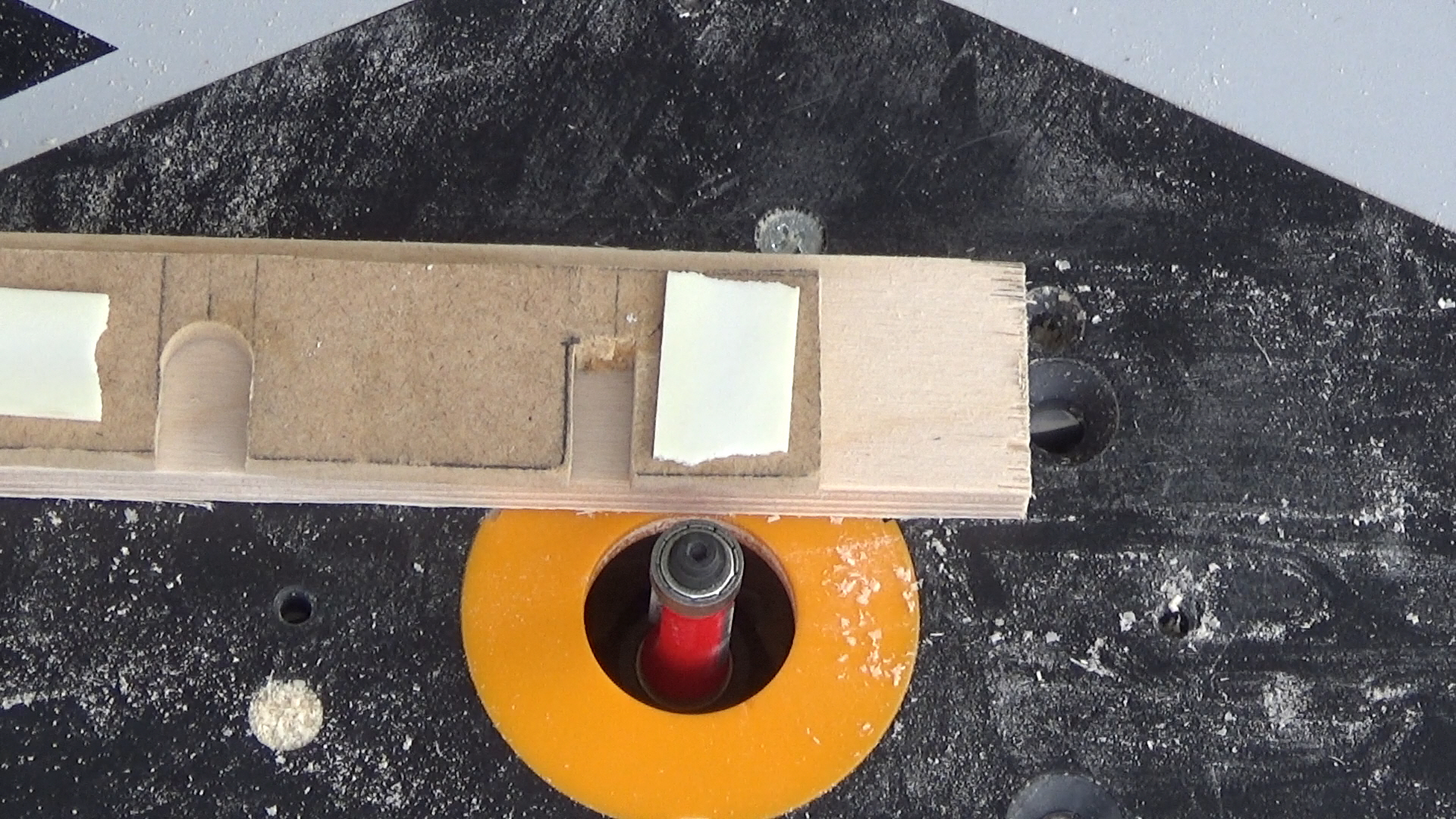
The ends need to be secured properly to prevent the template from slipping and causing your hands to possibly be thrown into a moving router. This has happened to people and you too could end up with a frame costing over $20,000 due to medical expenses from near loss of limbs.
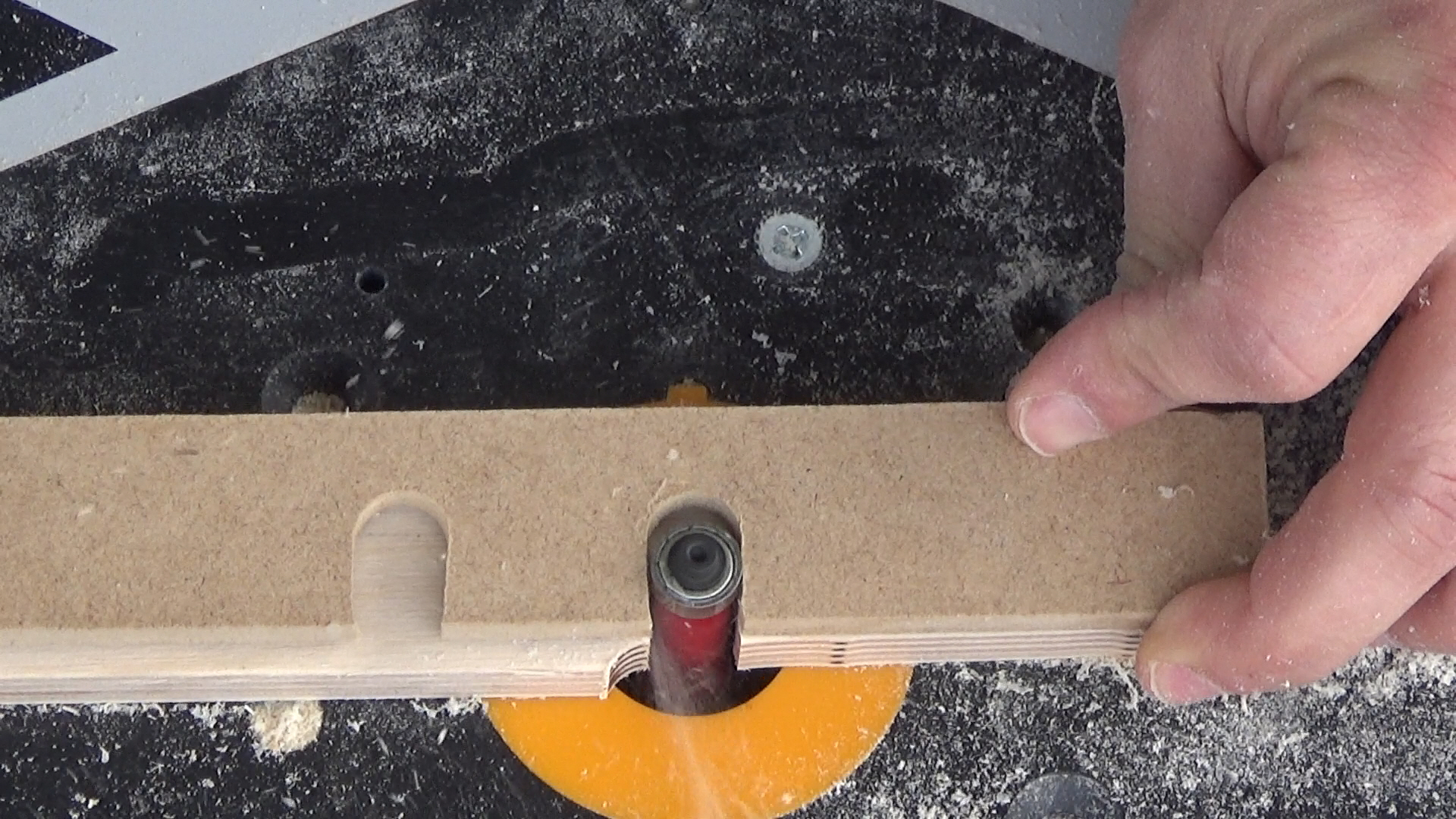
Cut slots using one to two templates, depending on their sizes.
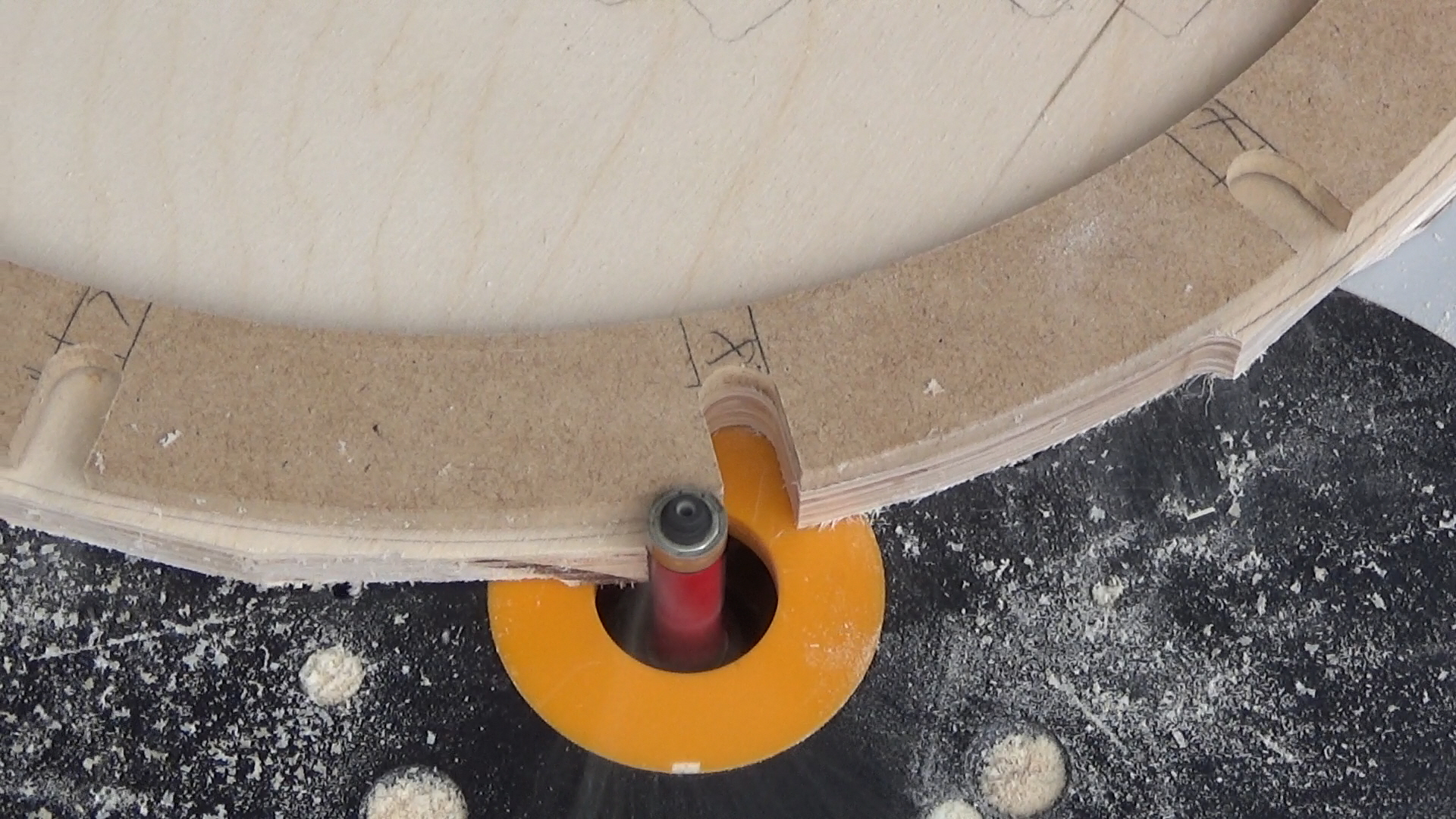
All slots should be cut from the same ring to guarantee the same alignment.